Crewsaver urges equipment caution
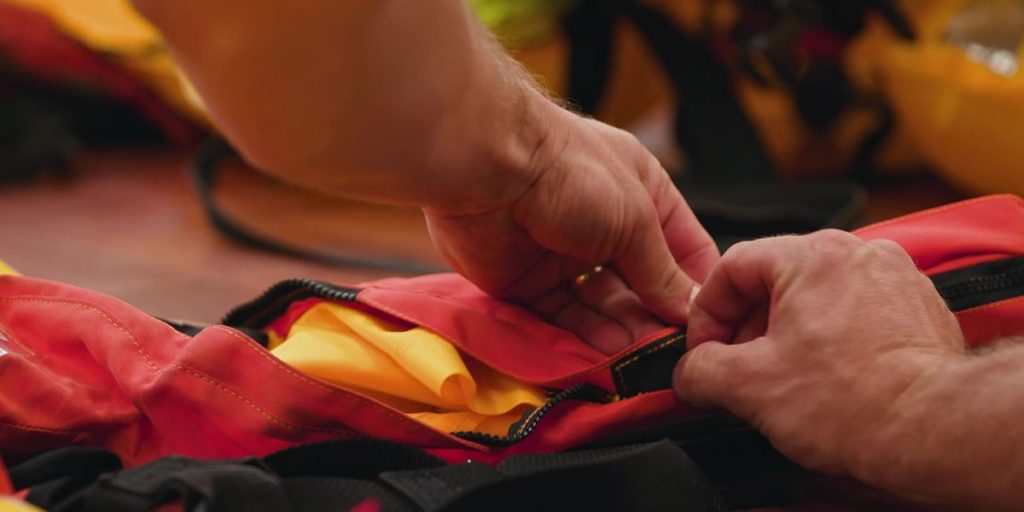
Crewsaver is advising boaters to ensure they carry out rigorous equipment checks before they put their vessels on the water following an easing of coronavirus lockdown rules.
“It is fantastic to see a recent easing of lockdown rules meaning that people can get back on the water,” says Matthew Bridge, Commercial Director of the Survitec brands Crewsaver and Yak. “Our message is do get out on the water but be safe and keep to the government guidelines to protect the emergency services. Before you head out, we strongly advise you to give your boat a good inspection and check your safety equipment.
“Lifejackets, flares, fire extinguishers, first aid supplies, and liferafts in particular, should be thoroughly checked before putting to sea to ensure they are damage-free and equipment is still in date.”
Bridge says it is quite possible that stowed lifejackets and other equipment have been sitting around in a damp environment or even submerged in a partially flooded locker.
“An obvious sign of a potential problem with a lifejacket is discolouration or corrosion. Lifejacket fabric should be checked for cuts, tears, abrasion and signs of damage caused by heat before manually inflating and leaving it for 12 hours. A lifejacket that is leaking will not hold its firmness and must be replaced,” he says. “Gas cylinders, lights, toggles and whistles should also be checked.”
Where lifejackets are fitted with Pro-Sensor or Hammar operating heads they will include status indicators, if these show red, then the cylinder should be checked to ensure it is fully charged. There should also be a green cap in the base of the capsule, but if this cannot be found, and a red dot is visible then the capsule could have been fired and must not be used.
“On our website we have how-to guides demonstrating how to re-arm your lifejacket. Alternatively, you can take your lifejacket to an approved Crewsaver service station and they can fit a new capsule onto your operating mechanism if required,” says Bridge, warning that the capsule must be replaced before use if it is out-of-date.
Lifejackets should be returned to the manufacturer or a qualified service agent for a full service every 12 months. Wear and contamination from salt spray, sand and dirt will all contribute to decreasing lifejacket efficiency.
Other equipment that should undergo inspection includes flares, the contents of first aid boxes and, where installed, liferafts.
“If fire extinguishers are onboard, regular inspections are advised to check for signs of damage, corrosion or leakage,” Bridge says. “Locking pins, seals and tamper indicators should be in place, and the pressure gauge must indicate the correct cylinder pressure range. In most cases, the correct pressure will be marked in green on the gauge.
“With regards to liferafts, the likelihood is that a canister or valise liferaft will remain properly sealed, but we do advise to check for any visible signs of seal damage and make sure the liferaft is within its due service date.
“These checks should be in addition to rigorous inspection of rigging, battery levels, bilge pumps, instruments and engines to make sure all is in working order before departing on any post-lockdown voyage,” he says. “If you look after your safety equipment it will look after you.”